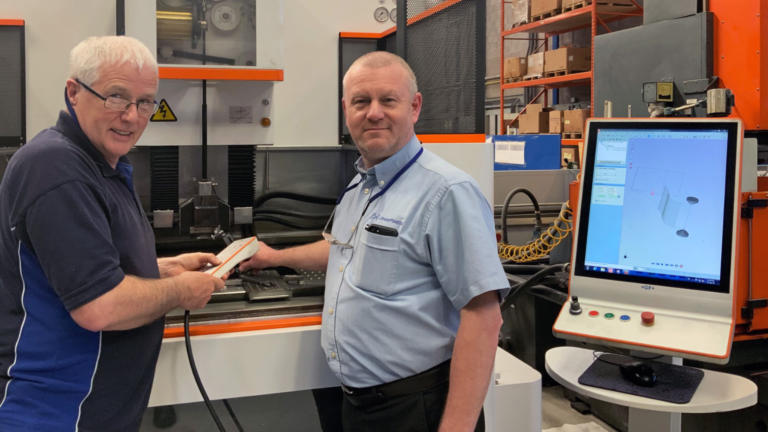
29th April 2019
Linear’s EDM skills ensure cost-effective mouldings
Linear Plastics, leading toolmaker and contract injection moulder, recently succeeded in saving a new customer a considerable amount of time and expense, thanks to the quick thinking and technical skillsets in its toolmaking department, together with the capabilities of its Charmilles-based Electrical Discharge Machining (EDM) investments.
Linear Plastics was presented ‘with a ‘fatal’ failure in one of our customer’s inherited mould tools, poor tool design at conception meant over time the main cavity die had cracked through a water circuit in an area which would have rendered the die a total loss, necessitating the costly remanufacture of a new one.
Simon Pugh — Process Improvements Manager
However, using the expertise of our tool design team we were able to redesign and provide a robust solution to the damaged area. Thanks to our Wire EDM capabilities we successfully cut away the cracked section of the main Die.
We then designed and manufactured a bespoke insert and successfully fitted it into the original mould tool cavity die. This tactic helped minimise production down time overall and kept the cost to our customer to an absolute minimum.’
Linear Plastics has continuously invested in its tool making and machining capabilities, primarily in order to complement and support its primary injection moulding business.
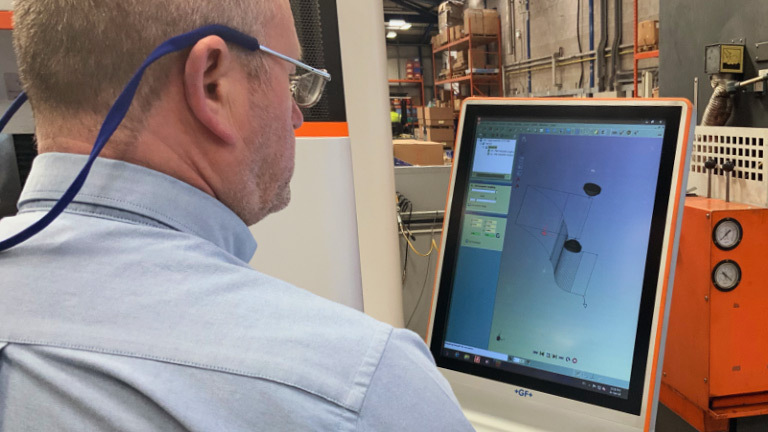
The company has a GF Cut 600E large capacity EDM Wire machine with integrated CAM (Fikus AC Cam) built into the machine’s touch screen control system. The machine is also hard wired into the Linear Plastics main server. This enables the company to have a direct link to the design and programming team. In order to further complement the EDM work Linear Plastics has two manually operated die sink machines; a Charmilles 4lc for large capacity work and a Charmilles Form 20 for the smaller and more intricate work.
The EDM Wire machine enables Linear Plastics to manufacture detailed and intricate electrodes required for the EDM Die Sink process which is used during the manufacture and repair of Mould Tooling and also allows us greater manufacturing freedom at Tool design stage.
These EDM Wire Erosion capabilities not only remove the need for subcontracting these services out, but are themselves available to market to toolmaking, engineering and plastics manufacturing communities.
Further recent investments at Linear Plastics include a Wittmann Battenfeld MacroPower 1000 tonne injection moulding machine (IMM) a Wittmann Battenfeld SmartPower 350 tonne IMM together with extensive capital spend on Hurco-based machining centres.